
ALTERNATING CURRENT FIELD MEASUREMENT (ACFM)
Introduction
Introduction ACFM is an electromagnetic technique. A sensor probe is placed on the surface to be inspected and an alternating current is induced into the surface. When no defects are
Present the alternating current produces a uniform magnetic field above the surface. Any defect present will perturb the current, forcing it to flow around and underneath the defect; this causes the magnetic field to
Advantages become non-uniform and sensors in the ACFM probe measure these field variations.
Two components of this magnetic field are measured one provides information about the depth or aspect ratio of the defect (s), and the other shows the positions of the defects’ ends. The two signals are used to confirm the presence of a defect and, together with a sizing algorithm, measure its length and depth.
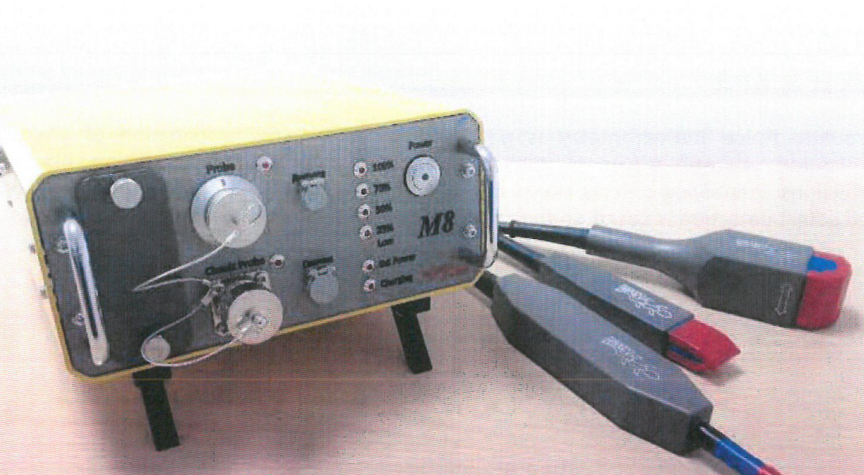
Applications
ACFM is particularly suited to the detection and sizing of fatigue cracks at the toes of welds, including all butt, fillet, node and nozzle welds. ACFM to inspect fillet welds in Mobile Offshore Drilling Units (MODUs) to detect any possible original fabrication hydrogen cracking present at weld toes.
It has also been successfully deployed in the laboratory in a joint industry project to detect stress corrosion cracking in duplex stainless-steel pipe welds.
- Offshore cranes
- Storage tanks floor & roof ‘lap’ joints
- Storage tank annular welds internal & external Vessel nozzles

Advantages
- The ability to detect defects through several millimeters of coating.
- Works equally well on plain material or welds, ferritic or non-ferritic metals. Can be used on hot surfaces, underwater, or in irradiated environments.
- Provides both depth and length information. Defects up to 25mm (1″) in depth can be sized accurately (providing that defect is open to surface).
- Rope access and ROV deployed. Real time evaluation of the weld area
